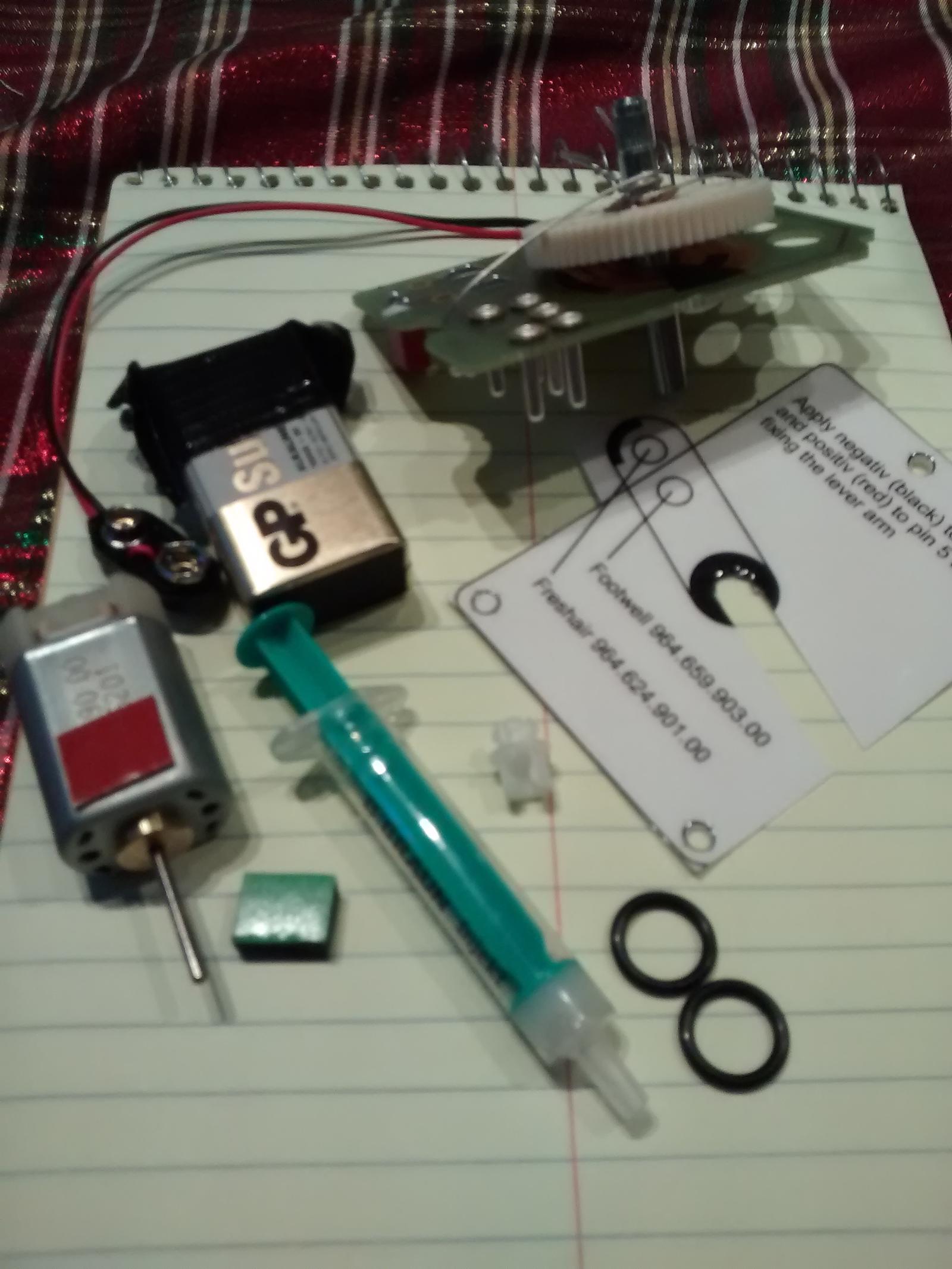
The HVAC system on a 993 uses several servo motors controlled by the Climate Control Unit (CCU) in the dash to adjust the temperature, switch from AC to heat, and control fresh air intake. The 964 shares two of the same servo part numbers as the 993 and has a slightly different layout as to the location of the servos. In any event, the insights below can be applied to the 964 although the part numbers may be different.
As our cars age, among other things, one or more of the servos will eventually fail. The usual failure mode involves burn marks on the rotary conductor board inside the servomotor. The motor stops when the arm reaches the position where the burn mark is located. This condition is detected by the CCU and the servo is disabled to protect the CCU until it is reset by having the ignition off >20 minutes or a battery disconnect. If you have an OBDC reader that can access the CCU Diagnostic Codes it will give you guidance as to if a servo has failed and which one it is.
Also, there is a great diagnostic sequence and a vast trove of other information for the HVAC system here as a good starting point if your HVAC system is not working properly: bergvillfx.com
Most of the servos are easy to get to, remove and rebuild. Two in the footwell walls and three under the cowl in the frunk. The internal parts are not serviceable but a rebuild kit can be ordered by email from Partisan-Autoteile for both the 993 & the 964 servos if you live in the Americas that basically replaces most of the internal parts. If you live in the EC or the UK one can ship their servos directly to them and they will install the kit for you. Shipping them out and back to and from the Americas is a bit expensive, slow, and these days unreliable so emailing them about the kits is the way to go. You won't find the kits on their website but they do offer them via email request. Also, in North America check pricing for a new service replacement servo at www.sunsetporscheparts.com as for certain servos, their price is only a little more than the cost of rebuilding your original servo. The various servo part numbers and locations can be found on this page.
Rebuilding the Fresh Air Servomotor 964.624.901.00, present on both the 964 & the 993
Here are my notes from my experience rebuilding the Fresh Air Servo-motor using new internal replacement parts from Partisan's kit. The other servos are very similar in construction so my notes should be useful when rebuilding them as well.
Read the instructions that came with the kit and my notes below before taking action.
- To remove the old Fresh Air servo (the one top-center in the frunk under the cowl):
- Leave the ignition off and the car's battery connected.
- Pop the long dust cover off the top of the cowl behind the firewall in the frunk, if your cover still has the rubber sealing blocks on its ends pressing against the frunk side walls pull them off first so they don't fall in the abyss behind your firewall.
- Unscrew and remove the two hold-down screws on the servo.
- With a screwdriver reach under the servo and pop the metal vent actuation arm off the servo's lever. If you lose the nylon lever capture clip the kit has a replacement one you should use anyway.
- Turn the ignition on. This will rotate the servo's external plastic lever arm 90 degrees so it lines up with a slot in its mounting frame allowing the arm to clear the frame and the servo to be lifted out. If your servo proves inactive (completely dead) at this point it will require further disassembly of the components around the servo to free up its mounting frame.
- Turn off the ignition, Unplug the servo from its harness
- You now have it in your hand for rebuilding.
- The instructions that come with the kit are very complete and include pictures however here are my suggestions and deviations.
- To avoid stressing the plastic housing when opening (splitting) it, use multiple toothpicks to hold the individual case latches on the sides of the case in the released position allowing the easy splitting of the case in half.
- The instructions speak of a nut that holds the servo's external plastic lever arm on the servo's rotating shaft. My unit had no such arrangement, possibly my unit was a later revision. My unit had what looked like a Phillips head hold-down screw at the end of the lever drive shaft holding the arm on. In my case, I carefully drilled the screw head off using a small drill bit to create a centering hole and a slightly larger bit to remove the screw head.
UPDATE Note 5/29/2021 - After looking at a footwell servomotor it may be the screw head is simply the stamped shape of the end of the spline shaft and may not need to be drilled off to slip the arm off the spline. Look at your unit closly to determin if this is the situation.
- I then used a punch to gently remove the shaft from the servo's external plastic lever arm using care not to crack or damage the twenty-five-year-old plastic arm.
- In the instructions, it speaks of positioning the large internal nylon gear referred to as the brush gear before reassembly. The final assembly step involves applying the supplied 9-Volt battery to the connector pins. If the brush gear is nominally placed somewhere in its correct operating range with battery power it will rotate the shaft the servo's external plastic lever arm will be reattached to in subsequent steps. If you encounter no movement when powering the pins reopen the case and reposition the brush gear close things up and try again.
- Do not use any power source other than a 9V transistor radio battery as the servomotor's internals are easily fried from too much voltage or amperage.
- Once the battery applied to the unit moves the shaft to the end of its travel it is in position to use the template in the kit to press on the servo's external plastic lever arm in the correct sweep position to the servo body.
- I pressed the external plastic lever arm back on its shaft using a C-clamp to press it on. I positioned the clamp so one end of the clamp rested on the arm where it needed to press over the shaft and the other end on the backside of the servo case against the other end of the shaft. In this way, no stress is placed on the case pressing on the arm. The arm does not press flush to the case so stop once it covers the shaft's splines and you encounter very slight increased resistance. Friction alone on the spline shaft has kept the arm in place for several years without the original Phillips head hold-down screw.
- To reinstall the servo using the uninstall instructions in reverse. It takes a little care and careful observation using screwdrivers and a hemostat, in my case, to position the metal vent actuation arm back into the nylon capture nut on the servo's external plastic lever arm.
Here are some instruction sheets from Partisan that came with their rebuild kits:
Notes for the two heater duct Footwell servos 993 624 325 00 (01)
- The servos and their flap mechanism are easily reached and removed with just a Phillips screwdriver.
- Ther is a star-shaped wheel on the end of the servomotor's shaft that acts as the linkage to the air flap in the duct.
- The servomotors star-wheel appears to be held in place by what looks like a screw on the end of the servomotor's shaft. It is not a screw, just the end of the spline shaft it is mounted to. The star-wheel can be gently pried up and off the spline on the end of the shaft.
- Taking the case apart involves releasing 8 catches around the periphery of the case. To avoid damaging the case I used one or more toothpicks to hold each catch open so the case can be separated with all the catches released simultaneously.
- When reassembling the servo preposition the new electric motor in the case bottom with gears in place and then press the circuit board down onto its electrical connection pins. Trying to attach it to the board before placing the board in the case will be problematic.
- Once the servo is assembled but before applying the star-wheel test it for movement, If you encounter no movement when powering the pins as discussed in the instructions reopen the servo's case and reposition the brush gear somewhere in its proper range of travel for its electrical contacts, close things up and try again.
- Once assembled and verified that it is moving when powered apply its star-wheel to its shaft using the supplied 9-volt battery & template for positioning then,
- Install the servomotor so its star-wheel is fully inserted in the flap's coupling
- loosely fit the servo mounting screws to the valve flap assembly then;
- Use the 9-volt battery with wire leads that came with the kit attached to test and adjust the servo valve and its linkage.
- Do not use any power source other than a 9V transistor radio battery as the servomotor's internals are easily fried from too much current.
- With the negative battery (black) lead on pin 4 of the assembled servo and the positive lead (red) on pin 5, it should open the footwell valve's flap for maximum hot airflow.
- Now switch polarity and put the red lead on post 4 and the black lead on post 5 closing the valve to the no-heat position. Observe that the valve closes fully'.
- If it does not and one can not get it to fully close using the play in the servo's mount screws to adjust it, then the servo's drive shaft star-wheel needs to be repositioned on its spline shaft one tooth or two to position it to fully close the valve.
- The purpose of making sure the left-hand and right-hand footwell seal completely is so the effectiveness of the AC is not diminished by warm air leaks in summer weather when running the AC.
Thank you to Geoff Bacci, a Rennlist member, for providing information and guidance for this page.
Andy
If you found this page informative return to the main page and bookmark it for future 993-related servicing, repair, and upgrading guidance & information. If it saved some time, aggravation, or even some coin consider a donation through the button on the top left margin of this page.
#993 #Heating #Ventilating # AC #A/C #servomotor #Climate Control Unit # CCU
#OBD #OBDC #OBDC-II #On board diagnostic